
Part feasibility refers to the assessment of whether a proposed part or component can be successfully manufactured according to specified requirements and constraints. It involves evaluating various factors to determine if the part design is viable and can be produced efficiently and economically.
The initial step involves reviewing the part design in detail. This includes examining dimensions, tolerances, material specifications, and functional requirements to ensure they align with manufacturing capabilities.
Evaluating the suitability of chosen materials for the part's intended function, considering factors such as mechanical properties, durability, corrosion resistance, and cost.
Ensuring that the part can meet quality standards and specifications required for its intended application. This involves evaluating dimensional accuracy, surface finish, strength characteristics, and adherence to regulatory requirements.

Benefits
Conducting a comprehensive part feasibility analysis is crucial for achieving efficient, cost-effective, and high-quality manufacturing processes.
Scalability and Flexibility
Compliance and Standards Adherence
Enhanced Design Optimization
Cost Savings
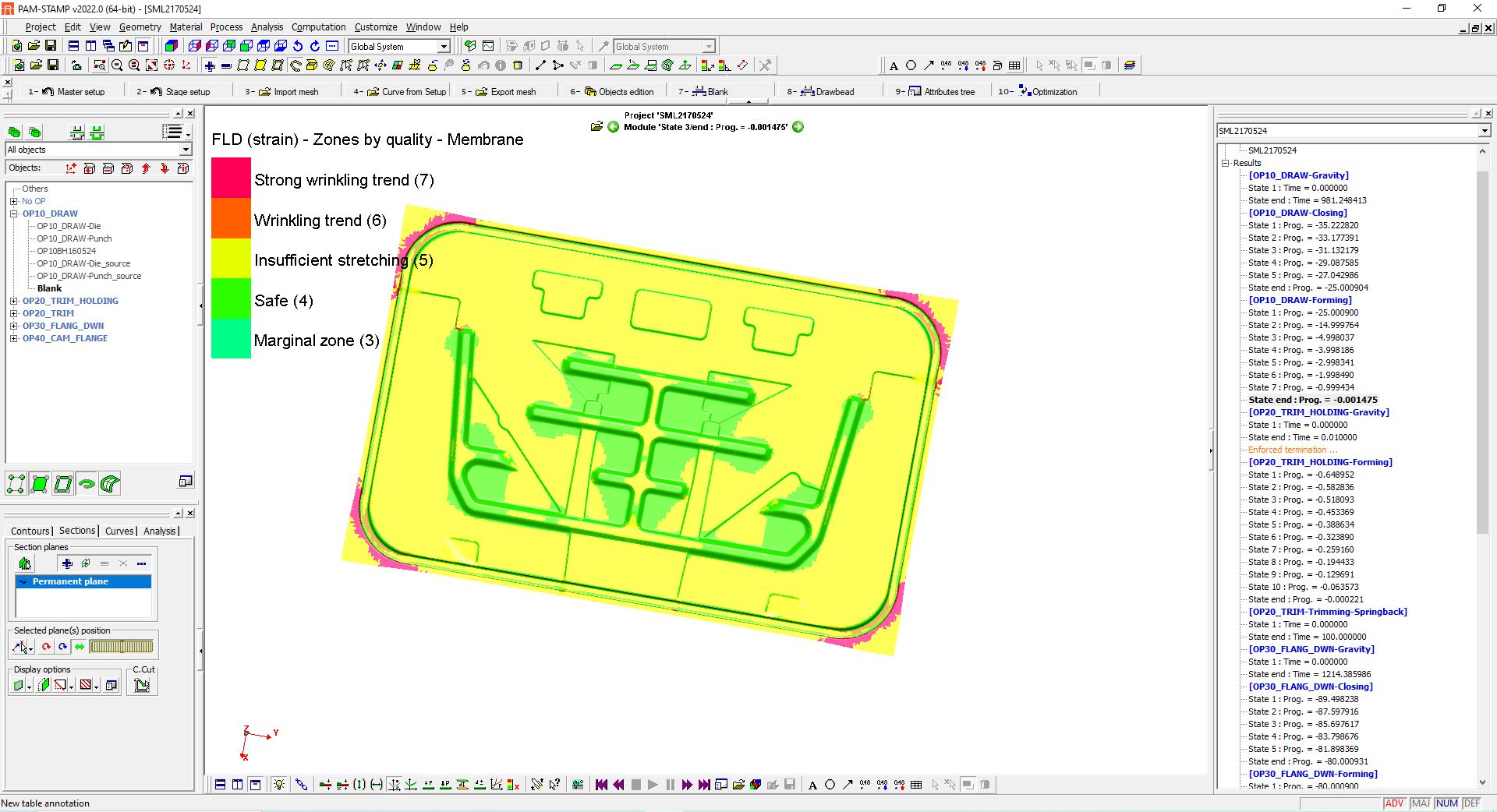
Softwares Used
We have latest and licensed software for designing the marvel which can outstand the ultra.
Pam Stamp ver2023
What are the key considerations in assessing part feasibility?
- Design Complexity: Evaluate if the design can be translated into a manufacturable part without compromising functionality or quality.
- Material Selection: Determine suitable materials based on mechanical properties, cost, availability, and manufacturing process compatibility.
- Manufacturing Processes: Assess which processes (e.g., machining, casting, molding) are suitable for producing the part efficiently and accurately.
- Tooling Requirements: Consider the need for specialized tools or equipment and their impact on production cost and lead time.
- Quality Standards: Ensure the part meets required quality standards and specifications.
- Cost and Budget: Evaluate the overall manufacturing cost, including material costs, labor costs, and overheads.
- Timeline: Assess whether production can be completed within the required timeframe.
How does material selection impact part feasibility?
- Mechanical Properties: Materials must meet the mechanical requirements (strength, stiffness, toughness) specified for the part.
- Manufacturability: Certain materials are better suited to specific manufacturing processes (e.g. draw, form).
- Cost: Material cost affects the overall product cost.
- Availability: Ensure the chosen material is readily available in the market.
What steps are involved in conducting a part feasibility?
- Review Requirements: Understand the design specifications and functional requirements of the part.
- Evaluate Design: Analyze the design for manufacturability, considering complexity, geometry, and material requirements.
- Select Manufacturing Process: Choose the appropriate manufacturing process based on design and material considerations.
- Simulate and Test: Use simulations or prototypes to validate feasibility and identify potential issues.
- Cost Analysis: Estimate manufacturing costs, including material, labor, tooling, and overhead costs.
- Documentation: Document findings, recommendations, and constraints for further design iterations or production planning.
How does part feasibility assessment contribute to overall project success?
- Alignment with Requirements: Ensures the final part design aligns with functional and performance requirements.
- Meeting Deadlines: Helps in planning and scheduling production activities to meet project timelines.
- Quality Assurance: Ensures parts are manufactured to meet quality standards and customer expectations.
- Cost Control: Helps in managing production costs within budget constraints.
- Customer Satisfaction: Delivers products that are reliable, cost-effective, and meet customer needs.
What are the key considerations in assessing part feasibility?
- Design Complexity: Evaluate if the design can be translated into a manufacturable part without compromising functionality or quality.
- Material Selection: Determine suitable materials based on mechanical properties, cost, availability, and manufacturing process compatibility.
- Manufacturing Processes: Assess which processes (e.g., machining, casting, molding) are suitable for producing the part efficiently and accurately.
- Tooling Requirements: Consider the need for specialized tools or equipment and their impact on production cost and lead time.
- Quality Standards: Ensure the part meets required quality standards and specifications.
- Cost and Budget: Evaluate the overall manufacturing cost, including material costs, labor costs, and overheads.
- Timeline: Assess whether production can be completed within the required timeframe.
How does material selection impact part feasibility?
- Mechanical Properties: Materials must meet the mechanical requirements (strength, stiffness, toughness) specified for the part.
- Manufacturability: Certain materials are better suited to specific manufacturing processes (e.g. draw, form).
- Cost: Material cost affects the overall product cost.
- Availability: Ensure the chosen material is readily available in the market.
What steps are involved in conducting a part feasibility?
- Review Requirements: Understand the design specifications and functional requirements of the part.
- Evaluate Design: Analyze the design for manufacturability, considering complexity, geometry, and material requirements.
- Select Manufacturing Process: Choose the appropriate manufacturing process based on design and material considerations.
- Simulate and Test: Use simulations or prototypes to validate feasibility and identify potential issues.
- Cost Analysis: Estimate manufacturing costs, including material, labor, tooling, and overhead costs.
- Documentation: Document findings, recommendations, and constraints for further design iterations or production planning.
How does part feasibility assessment contribute to overall project success?
- Alignment with Requirements: Ensures the final part design aligns with functional and performance requirements.
- Meeting Deadlines: Helps in planning and scheduling production activities to meet project timelines.
- Quality Assurance: Ensures parts are manufactured to meet quality standards and customer expectations.
- Cost Control: Helps in managing production costs within budget constraints.
- Customer Satisfaction: Delivers products that are reliable, cost-effective, and meet customer needs.